How Safety Tools Allmet Secured EX Maintenance on Aker FPSO Dhirubhai-1
Background and Challenge
FPSO Dhirubhai-1, previously owned by Aker and operated offshore in India, required extensive maintenance work in EX zones, without compromising production or safety. Surface treatment was carried out without the need for a hot work permit.
Safety and EX Compatibility Requirements
The work had to be performed in hazardous areas (EX zone 1 and 2), which excluded the use of traditional angle grinders and heat-generating tools.
The solution had to be:
-
Spark-free and cold
-
DNV-certified for EX use
-
Suitable for continuous operation without interruptions
Certification and Approvals
-
The tools were DNV-certified for use in EX zone 1 and 2
-
The system required no hot work permit
-
Fully compliant with applicable HSE standards for offshore operations
The Solution: EX-Certified Tools from Safety Tools Allmet
Safety Tools Allmet supplied complete sets of cold solutions, including:
This enabled mechanical surface treatment according to ST 3 standard without heat generation or spark formation.
Work Performed and Scope
The tools were used for surface treatment of 6,020 m² out of a total of 17,195 m² in the project. The areas included:
-
Gas compressor areas
-
Process modules
-
Pump rooms
-
Under-deck piping systems
-
Helideck and turret structure
The coating system consisted of 3 layers of Jotun Jotacote Universal, applied using roller, brush, and airless spray. Total film thickness was 350 microns.
Results and Efficiency
-
Productivity: 23.5 m² per day (including scaffolding work)
-
No safety incidents reported during the project period (2 years)
-
Full customer satisfaction, documented through feedback forms
Customer Feedback
“Very good supervision and excellent QHSE compliance.”
— Chief Officer, Dhirubhai-1
Conclusion
Safety Tools Allmet delivered a complete and safe solution for EX maintenance on board Aker FPSO Dhirubhai-1. Our tools enabled continuous operation, eliminated the need for hot work permits, and set a new standard for EX maintenance offshore.
This case demonstrates that technical safety and performance can be combined — when you use the right tools.
Below you will find images of the finished result after surface preparation using Safety Tools Allmet’s cold solutions.
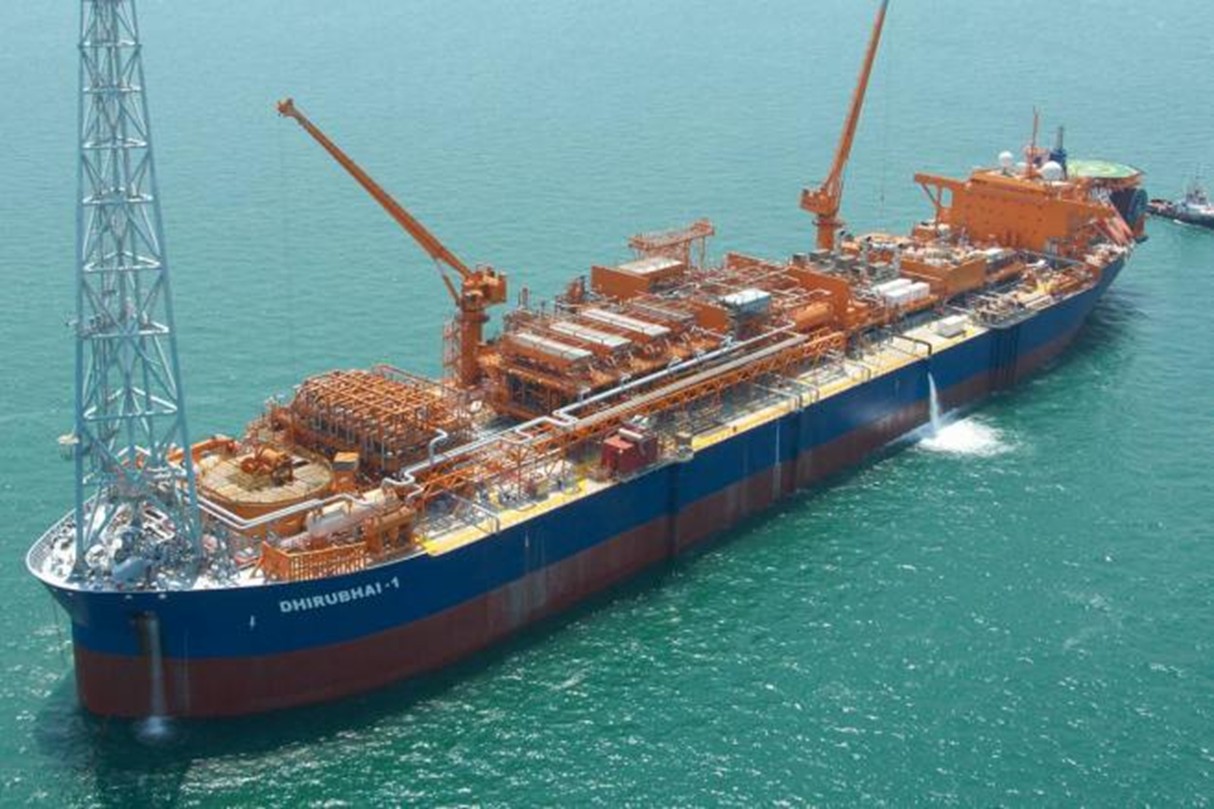
DHIRUBHAI-1
After-final-coat-in-U-71area
After-final-coat-in-U-70-2
After-final-coat-in-U-70
After-final-coat-in-U-30-4
After-final-coat-in-U-30-3
After-final-coat-in-U-30-2
After-final-coat-in-U-30
After-final-coat-in-U-20-solar-area
After-final-coat-in-U-10area
After-final-coat-in-U-10-2
After-final-coat-in-P-112-
After-final-coat-in-P-11
After-final-coat-in-P-10top-side-2
After-final-coat-in-P-10top-side
After-final-coat-in-P-10area-2
After-final-coat-in-P-10area
After-final-coat-in-P-10-3
After-final-coat-in-Gas-Compressor-Area-3
After-final-coat-in-Gas-Compressor-Area-2
After-final-coat-in-Gas-Compressor-Area
After-final-coat-in-gas-compresor-area-2
After-final-coat-in-F-10-3
After-final-coat-in-F-10
After-final-coat-below-main-deck
After-final-coat-on-top-side-of-gas-compressor-area-3
After-final-coat-on-top-side-of-gas-compressor-area-2
After-final-coat-on-top-side-of-gas-compressor-area
After-final-coat-on-solar-in-U-70
After-final-coat-on-solar-funnel-in-U-70
After-final-coat-on-P-40-P-41area
After-final-coat-in-U-71area-3
After-final-coat-in-U-71area-2