Introduction to Composite Repairs
Composite technology has been around for more than a decade, representing an affordable and timesaving option for pipe rehabilitation. The introduction of codes and standards, ASME↵ and ISO↵ engineering standards has helped composite repairs gain wider acceptance in the industry as an effective solution for restoring pipeline integrity and structural strength.
Composites can perform repairs with no disruption to operations. More and more pipeline operators are making these systems part of their pipeline integrity programs for repairing corrosion, dents, and other defects in their steel-piping systems.
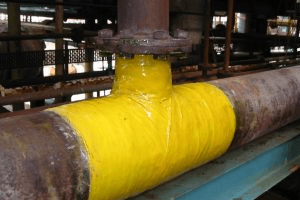
Adhesives
An important project is adding to industry knowledge about the adhesives used in several currently available composite repair systems. This is critical information, since adhesives not only bond the repair to the substrate; they also bond individual layers of the repair to each other. If the bond between layers is not adequate, the load will not be transferred from the pipe to the repair.
The integrity of composite repairs depends largely on how well the compounds have adhered to the surface of the pipe. We have studied that the profile of the prepared surface significantly affects the adhesion integrity of the composite repairs. However, you cannot shut down many classified sites to use hot works surface preparation methods. Such as conventional grinding and sandblasting. Consequently, many of the repairs were not performed satisfactorily due to poor adhesion to the unclean surface.
Safety Tools Allmet
- ATEX for zones 1 & 2. (NO hot work permits required in these two areas), Certified by DNV, and classified as a Cold Working Tool.
- No Hot sparks. (Prevention of spot corrosion caused by conventional cutting and grinding)
- Low heat. (average 30C to 60C grinding steel) – you can immediately place your hands on the steel after working on the substrate.
In summary, for the above three pointers, there is no requirement for the erection of habitats and fire guards and no need to cover expensive equipment nearby when performing the cutting/grinding task. It is possible to work near your colleagues, thus improving productivity.
Even more benefits when using Safety Tools Allmet
- No release of Isocyanides. when you grind or cut through the polyurethane
- Low Noise. (<85 dBA) – excellent for operators, no incidence of NID, and no requirement for earplugs for most countries.
- No Dangerous Sharp Splinters. – you can even place your hands just 1mm away without the risk of exposure to sparks or splinters.
- Low Vibration. (Average <2.5 m/s) – Getting the work done quickly without much operator fatigue
- Roughness Profile 40 – 75 microns. – extensively independently tested for surface adhesion by International Paint, Jotun, Chevron, and Weatherford
- Long tool life.
- Excellent anchor profile on the prepared surface.